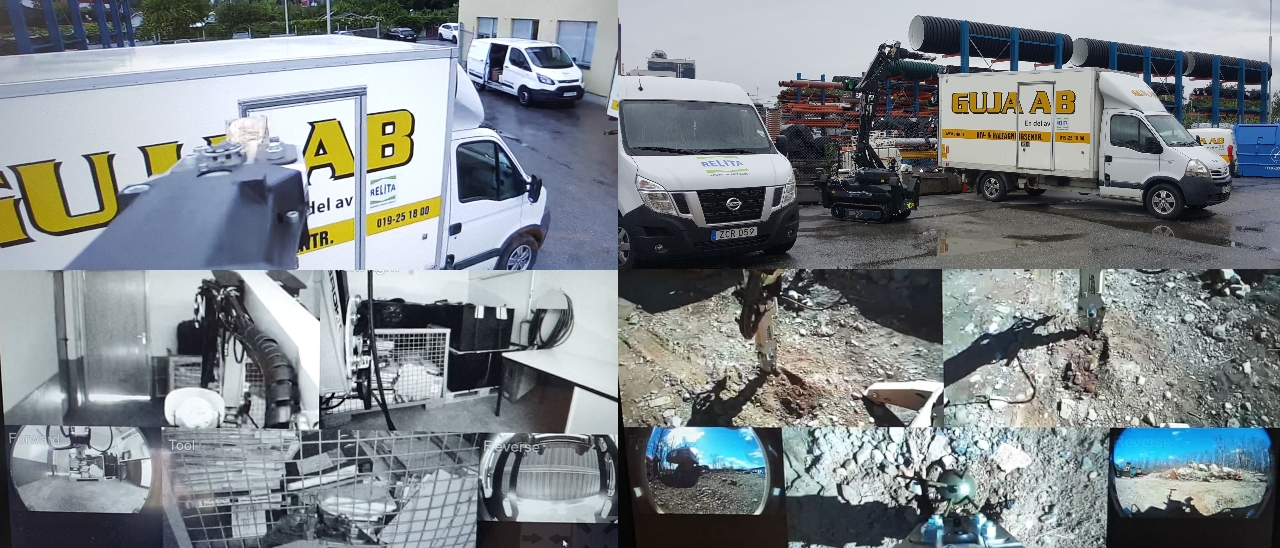
Data-Link and Sensors
MX-Series – Real-Time Encrypted Digital Data-Link
The real-time communication between the Operator and the Robot is centred around one extremely robust digital, MIL-Std data-link with two types of encryption either 56bit or the ***AES256 bit hardware encryption. The radio is not only robust, but also very powerful** and designed for non line of sight operation. Already the very basic setups, without any options, are equipped with the data-link specified at + 1.000m (LoS) communication.
The system can be supplied with an OPTIONAL MIL-Std Optical Fibre Module (OFM). This is easily mounted if/when needed and can thereafter be removed. Connecting the optical fibre to the CBB (Communication Break out Box) also disconnects the radio physically from power and communication, making it impossible to make a mistake such as leaving the radio on when operating in areas possibly sensitive to radio-traffic. | ![]() |
The basic data-link consists of the Platform Communication Module (PCM) integrated on the robot and the separate Transmitting/Receiving Module (TRM) on the operator side. The PCM includes the radio module and the Communication Break out Box (CBB). The CBB is the communication hub of the robot. Here the standard sensors are connected, but more important this is the open interface for connecting additional sensors and tools through various supported protocols such as RS, CAN and our preferred Ethernet.
MX-Series – Modular Multi Sensor Design
Vision
The standard digital EO-cameras of the MX-series provides the operator with close to optimal video quality, partially due to the use of the latest imbedded video compression. The camera also has an automatic IR-filter that switches between day and night-mode.
However, it is the cameras positioning, module configurations, digital UDP data link and display software that makes the setup truly unique.
In basic configuration the MX is equipped with five cameras in protected positions around the machine.
One is located on the mounting plate of the tool, but it is also possible to reposition it depending on the tool being used at the time, there is also an additional LED-light that can be remotely turned on/off independent of the other lights. This feature is integrated with all LED-lights on the MX-Series.
Two cameras are located on independent pan/tilt heads operated by joystick from the OCM-Operator Control Module, giving the operator two separate 360 degree pan/tilt views. The reason for using pan/tilt heads instead of cameras with this function integrated is reliability, PTZ-cameras are more sensitive to vibrations and rough environments. Our solution also makes replacement and upgrades easier. Take one camera out by disconnecting the cable and replace! The pan/tilt camera modules are also placed as far apart as possible, giving the operator a much better sense of depth (3D) when operating remotely on 2D-screens. The rear left module is also equipped with a separate LED-light. The front right module is supported by the two main LED-lights integrated in the turret of the MX. Two wide angle drive cameras are positioned in the front and back of the platform to support the operator in drive mode. The wide angle cameras were added on request from end users testing the system. They found this feature very helpful when manoeuvring in narrow and delicate environments, they allow the operator to see the complete front and back of the platform helping to judge distance, something that is otherwise difficult in 2D. The front and rear cameras have their own LED-lights, again all remotely and individually controlled. |
![]() |
Audio
The MX-Series is equipped with two way audio communication, this is to provide the operator with as much feed back from the robot as possible during non line of sight operation. Being able to hear the system working while watching real time images is a great help. In a mission it can also be important to communicate with the people close to the robot, for example in a rescue situation operators can talk to wounded or trapped people and explain the situation, helping to keep them calm.
The system can be upgraded with the OPTIONAL PTM – Pc-Tablet Module for two operator support, this system includes one extra pair of headphones with microphone so that the two operators can communicate with each other and/or with externals through the loudspeaker and microphone on the robot.
Other sensors
In addition to vision and audio, other sensors are monitoring the robot itself, such as temperature, oil pressure and remaining fuel, this information is sent back to the operator to support the mission. The system can be further equipped with various sensors depending on the needs of the organisation operating it.
Daylight Video | Night-mode Video |
Operator Modules |
*Approximative and depending on tool
**the use of the radio is in most countries subject to local approval
***256 bit encryption is subject to export regulations